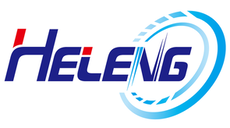
HELENG: High-efficient, Expandable, Light Engine aNd Generator
- RTE: Rocket Turbine Engine Patents :
- US Patent No.: US 11,035,298 B1 Title: TURBINE ENGINE SYSTEM Jun. 15 2021
- US Patent No.: US 12,060,840 B2 Title: TURBINE ENGINE SYSTEM Aug. 13 2024 (CIP)
HELENG's Mission:
1. Challenge the current All-Electric EV industry with HELENG's patented and lab tests validated Rocket Turbine Hybrid Engine technologies which will improve the mpg (miles per gallon) significantly, especially for trucks.
2. Build High-efficient , light, compact and quiet generators and "Zero-Carbon" compact size power-plants.
Rocket Turbine Hybrid Engine (RTHE) technologies:
Abstract:
The patented Turbine Engine System, named the Rocket Turbine Engine (RTE), is a highly efficient, powerful, compact, lightweight, mechanically simple, and quiet turbine engine. No water-cooling system, oil changes, or starter motor are required for RTE operations. The RTE couples with off-the-shelf Axial Flux Motors (AFMs) to form various high-power density and compact hybrid engines for vehicles ranging from passenger cars to semi-trucks. The RTE-AFM combination hybrid engines are designed to significantly improve miles per gallon (MPG), especially for trucks. Both the RTE and AFM have pancake shapes and can be co-shafted to expand their power output. Since both the RTE and AFM have similar shapes and compact sizes, these Hybrid Engine Systems can be easily expanded and adapted to meet most automobile engine requirements. An RTE-AFM hybrid engine can be directly connected to an existing transmission (gearbox), instantly converting any truck into a hybrid-engine truck.
Background
All-electric vehicles face several challenges:
Basically, hybrid vehicles combine an electric motor for starting with a piston-based Internal Combustion Engine (ICE) for cruising. The main advantage of hybrid vehicles is their ability to convert kinetic energy into electricity when braking, recharging the battery in the process. However, piston-engine-based hybrid systems have drawbacks:
In contrast to piston engine, the patented Turbine Engine System named Rocket Turbine Engine (RTE) is a highly efficient, powerful, compact, lightweight, mechanically simple, and quiet turbine engine. No liquid-cooling system, no oil changes and no starter motor are required for RTE operations. RTE has more than 60% thermal efficiency.
RTE couples with off-the-shelf Axial Flux Motors (AFMs) to form various high-power density and compact hybrid engines for vehicles ranging from passenger cars to semi-trucks. The RTE-AFM combination hybrid engines are designed to significantly improve MPG (Miles Per Gallon) of automobile, especially for trucks. Both RTE and AFM have pancake shapes and can be co-shafted to expand their power output. Since both RTE and AFM have similar shapes and compact sizes, these Hybrid Engine Systems can be easily expanded to meet most automobile engine requirements.
1. Challenge the current All-Electric EV industry with HELENG's patented and lab tests validated Rocket Turbine Hybrid Engine technologies which will improve the mpg (miles per gallon) significantly, especially for trucks.
2. Build High-efficient , light, compact and quiet generators and "Zero-Carbon" compact size power-plants.
Rocket Turbine Hybrid Engine (RTHE) technologies:
Abstract:
The patented Turbine Engine System, named the Rocket Turbine Engine (RTE), is a highly efficient, powerful, compact, lightweight, mechanically simple, and quiet turbine engine. No water-cooling system, oil changes, or starter motor are required for RTE operations. The RTE couples with off-the-shelf Axial Flux Motors (AFMs) to form various high-power density and compact hybrid engines for vehicles ranging from passenger cars to semi-trucks. The RTE-AFM combination hybrid engines are designed to significantly improve miles per gallon (MPG), especially for trucks. Both the RTE and AFM have pancake shapes and can be co-shafted to expand their power output. Since both the RTE and AFM have similar shapes and compact sizes, these Hybrid Engine Systems can be easily expanded and adapted to meet most automobile engine requirements. An RTE-AFM hybrid engine can be directly connected to an existing transmission (gearbox), instantly converting any truck into a hybrid-engine truck.
Background
All-electric vehicles face several challenges:
- Time-consuming recharging process
- Limited availability of charging stations
- Risk of uncontrollable fires if the battery ignites
- Requirement for large, expensive, and heavy lithium batteries
Basically, hybrid vehicles combine an electric motor for starting with a piston-based Internal Combustion Engine (ICE) for cruising. The main advantage of hybrid vehicles is their ability to convert kinetic energy into electricity when braking, recharging the battery in the process. However, piston-engine-based hybrid systems have drawbacks:
- Complex and bulky mechanical design
- Thermal efficiency of only about 35% due to piston friction and wasting much energy on none shaft driving force for 4-stroke mechanism because one ignition has only one quarter of power driving the shaft.
- Numerous components, including crankshaft, camshaft, timing belt, cooling system, starter motor, lubrication system, and drivetrain, making maintenance challenging
In contrast to piston engine, the patented Turbine Engine System named Rocket Turbine Engine (RTE) is a highly efficient, powerful, compact, lightweight, mechanically simple, and quiet turbine engine. No liquid-cooling system, no oil changes and no starter motor are required for RTE operations. RTE has more than 60% thermal efficiency.
RTE couples with off-the-shelf Axial Flux Motors (AFMs) to form various high-power density and compact hybrid engines for vehicles ranging from passenger cars to semi-trucks. The RTE-AFM combination hybrid engines are designed to significantly improve MPG (Miles Per Gallon) of automobile, especially for trucks. Both RTE and AFM have pancake shapes and can be co-shafted to expand their power output. Since both RTE and AFM have similar shapes and compact sizes, these Hybrid Engine Systems can be easily expanded to meet most automobile engine requirements.
RTHE SUMMARY:
Rocket Combustion Chamber (RCC)
The Rocket Combustion Chamber (RCC) is a crucial part of the RTE. Hundreds of RCC lab tests have been conducted, resulting in successful outcomes. The RCC design patent was approved by USPTO in August 2024 as a Continuation-In-Part (CIP) to the original Turbine Engine System Patent from June 2021
Similar to a rocket engine, the RCC utilizes Newton's Third Law of Motion: "For every action, there is an equal and opposite reaction". While a rocket engine has about 60% thermal efficiency for thrust, the RCC directs all energy and force to the spherical shape of the turbine blade at the tangent line direction to maximize shaft rotation power, i.e., torque
An RCC further comprises:
The air compressor of the RCC not only provides air for combustion but also serves as an air-cooling system for the entire turbine engine when needed. The EFI high-pressure fuel injection also contributes some cooling effect for the RCC.
RTE vs Rocket Engine
According to Charles's Gas Law, for every 100°C increase in temperature, gas volume increases by 36.6%. A typical gasoline internal combustion chamber reaches about 2,500°C when ignited, causing the gas volume to increase 8.33 times. Unlike a typical rocket engine that disperses high-temperature gas flame after generating thrust, the RTE retains residual energy to be confined in a "rotary-piston" to continue turning the turbine/shaft in a most efficient and direct way until the hot air is directed to the exhaust pipe. The faster the turbine spins, the faster hot air can reach the exhaust pipe. This is a major advantage of the RTE over conventional rocket engines.
RTE vs Gas Turbine Engine
A regular gas turbine engine has two groups of turbines, each group comprising many stages of turbines to improve its efficiency. The front group of turbines is for the air compressor to take in a large amount of air for combustion. The rear group of turbines is to extract as much combustion thrust power as possible to turn the shaft. All these turbine groups comprise many complicated turbine blades mechanically because the combustion force is facing the angled turbine blade and is perpendicular to the shaft motion (not efficiently). In contrast, the RTE is a single turbine system with combustion power aligned to the shaft rotation direction. The longer the RTE blade arm, the more torque the RTE generates.
RTE vs Piston Engine
A traditional piston engine has 4 strokes for an ignition cycle to turn the shaft: 1) Air intake, 2) Air compression, 3) Ignition, and 4) Exhaust. Only one quarter of an ignition cycle contributes power to the shaft, while the other three quarters of force work on the remaining three strokes through the crankshaft in an ignition cycle. The compression stroke, in particular, requires more power. There are camshaft valves with spring resistance forces and a timing belt that need power to drive in order to maintain engine ignition cycle synchronization. In contrast, an RTE can ignite all its Rocket Combustion Chambers (RCCs) simultaneously and contribute most of the combustion power to the shaft on each iginition.
Although a piston engine can run very fast, the friction at high speed is also very high, not to mention the heat it generates and the air explosion noise it produces. A piston engine requires a starter motor to start and requires regular oil changes. A liquid cooling system is also required for a piston engine. In contrast, the RTE is frictionless (because only bearings required) and quiet. No oil changes or liquid cooling system are required for RTE operation.
RTE-AFM Hybrid Engines
The RTE couples with off-the-shelf Axial Flux Motors (AFMs) to form various high-power density and compact hybrid engines. These engines are suitable for vehicles ranging from passenger cars to semi-trucks and are designed to significantly improve Miles Per Gallon (MPG), especially for trucks. There is a ratio gear between the RTE and AFM shaft due to the RPM (rounds per minute) disparity. There is a clutch to disengage the RTE-AFM operation from wheel turning, especially for electric generator operation. There is also a ratio gear between the RTE-AFM shaft and wheel drivetrain shaft because of the RPM disparity.
RTE-AFM Hybrid Engine Key Features:
RTE-AFM Hybrid Engines Operation Modes:
Rocket Combustion Chamber (RCC)
The Rocket Combustion Chamber (RCC) is a crucial part of the RTE. Hundreds of RCC lab tests have been conducted, resulting in successful outcomes. The RCC design patent was approved by USPTO in August 2024 as a Continuation-In-Part (CIP) to the original Turbine Engine System Patent from June 2021
Similar to a rocket engine, the RCC utilizes Newton's Third Law of Motion: "For every action, there is an equal and opposite reaction". While a rocket engine has about 60% thermal efficiency for thrust, the RCC directs all energy and force to the spherical shape of the turbine blade at the tangent line direction to maximize shaft rotation power, i.e., torque
An RCC further comprises:
- A funnel shape of combustion chamber with narrow nose as the rocket nuzzle
- An air compressor/fan for fuel combustion
- An Electronic Fuel Injector (EFI) for high-pressure fuel injection
- A sparkplug and a coil for the sparkplug for combustion
- An Air Intake Valve (AIV) similar to heart valves that prevent blood backflow
The air compressor of the RCC not only provides air for combustion but also serves as an air-cooling system for the entire turbine engine when needed. The EFI high-pressure fuel injection also contributes some cooling effect for the RCC.
RTE vs Rocket Engine
According to Charles's Gas Law, for every 100°C increase in temperature, gas volume increases by 36.6%. A typical gasoline internal combustion chamber reaches about 2,500°C when ignited, causing the gas volume to increase 8.33 times. Unlike a typical rocket engine that disperses high-temperature gas flame after generating thrust, the RTE retains residual energy to be confined in a "rotary-piston" to continue turning the turbine/shaft in a most efficient and direct way until the hot air is directed to the exhaust pipe. The faster the turbine spins, the faster hot air can reach the exhaust pipe. This is a major advantage of the RTE over conventional rocket engines.
RTE vs Gas Turbine Engine
A regular gas turbine engine has two groups of turbines, each group comprising many stages of turbines to improve its efficiency. The front group of turbines is for the air compressor to take in a large amount of air for combustion. The rear group of turbines is to extract as much combustion thrust power as possible to turn the shaft. All these turbine groups comprise many complicated turbine blades mechanically because the combustion force is facing the angled turbine blade and is perpendicular to the shaft motion (not efficiently). In contrast, the RTE is a single turbine system with combustion power aligned to the shaft rotation direction. The longer the RTE blade arm, the more torque the RTE generates.
RTE vs Piston Engine
A traditional piston engine has 4 strokes for an ignition cycle to turn the shaft: 1) Air intake, 2) Air compression, 3) Ignition, and 4) Exhaust. Only one quarter of an ignition cycle contributes power to the shaft, while the other three quarters of force work on the remaining three strokes through the crankshaft in an ignition cycle. The compression stroke, in particular, requires more power. There are camshaft valves with spring resistance forces and a timing belt that need power to drive in order to maintain engine ignition cycle synchronization. In contrast, an RTE can ignite all its Rocket Combustion Chambers (RCCs) simultaneously and contribute most of the combustion power to the shaft on each iginition.
Although a piston engine can run very fast, the friction at high speed is also very high, not to mention the heat it generates and the air explosion noise it produces. A piston engine requires a starter motor to start and requires regular oil changes. A liquid cooling system is also required for a piston engine. In contrast, the RTE is frictionless (because only bearings required) and quiet. No oil changes or liquid cooling system are required for RTE operation.
RTE-AFM Hybrid Engines
The RTE couples with off-the-shelf Axial Flux Motors (AFMs) to form various high-power density and compact hybrid engines. These engines are suitable for vehicles ranging from passenger cars to semi-trucks and are designed to significantly improve Miles Per Gallon (MPG), especially for trucks. There is a ratio gear between the RTE and AFM shaft due to the RPM (rounds per minute) disparity. There is a clutch to disengage the RTE-AFM operation from wheel turning, especially for electric generator operation. There is also a ratio gear between the RTE-AFM shaft and wheel drivetrain shaft because of the RPM disparity.
RTE-AFM Hybrid Engine Key Features:
- Both RTE and AFM have pancake shapes and can be co-shafted to expand power output.
- The similar shapes and compact sizes of RTE and AFM allow for easy expansion to meet most automobile engine requirements.
- Trucks can be converted to hybrid engine vehicles by directly connecting an RTE-AFM hybrid engine main drive shaft to an existing transmission gearbox.
RTE-AFM Hybrid Engines Operation Modes:
- Vehicle Start: Normally, AFM uses battery power to start and rapidly accelerate the vehicle because AFM can generate very high torque. For example, YASA 750R can produce up to 200 kW peak power and 790 Nm torque.
- Vehicle Cruising: In this mode, the vehicle uses RTE to maintain speed. Since RTE has more than 60% thermal efficiency, good mpg (miles per gallon) can be achieved. A gasoline piston engine-based hybrid vehicle can only reach 35% thermal efficiency. A diesel piston engine-based truck can reach 30%-45% practical thermal efficiency.
- Vehicle Braking: When the driver hits the brake or releases the gas pedal, the wheel's kinetic energy will drive the AFM to generate electricity and recharge the battery for reuse. This operation will save about 10% fuel.
- Dual Power Mode: When the vehicle goes uphill and requires very large power, both RTE and AFM together can contribute more power to the vehicle.
- AFM Battery Low: While the vehicle is cruising, when the AFM battery is dangerously low, RTE can generate power for both vehicle movement and recharge the battery through AFM simultaneously.
- Stand-Alone Generator: An additional benefit of RTE-AFM hybrid engine vehicles is that the hybrid engine vehicle can serve as a mobile, large-capacity, high-efficiency, and quiet electric generator.
- Reverse Mode: For front-wheel RTE-AFM hybrid engine, the reverse mode is required for vehicle to move backward. In this mode the Inverter/Converter electronic box can drive the AFM to rotate reversely. The RTE-AFM hybrid engine for truck does not require reverse mode because the transmission gearbox has the reverse gear function.